4 Principle
A pipe of specified length is placed in a liquid bath or air oven at a specified temperature for a specified time .
A marked length of this portion of pipe is measured, under identical conditions, before and after heating. The reversion is calculated as a percentage of the change in length in relation to the initial length. The surface appearance of the test piece shall not be changed after heating.
5 Apparatus
5.1 Heated liquid bath, thermostatically controlled at the temperature, TR, as specified in Table 1, unless
Otherwise specified by a referring standard.
The volume and agitation of the bath shall be such that the temperature remains within the specified
temperature range when the test piece is immersed.
The liquid chosen should be stable at the specified temperature and should not otherwise affect the plastic material.
NOTE Glycerine, glycol, mineral oil free from aromatic hydrocarbons, or a solution of calcium chloride are suitable, but any other liquid in line with these recommendations can be used.
5.2 Air oven, thermostatically controlled such that it operates at the temperature, TR, as specified in
Table 1, unless otherwise specified, and capable of re-establishing this temperature within 15 min of the
introduction of the test pieces. The oven shall be equipped with a thermostat capable of maintaining TR to a permissible deviation of ± 2 °C.
5.3 Ancillary equipment
5.3.1 Device to hold the test piece(s) within the heating bath or oven in accordance with Clause 7.
5.3.2 Thermometer, with an accuracy to within ± 0,5 °C.
6 Preparation
6.1 Test piece
Immediately after extrusion, the sample of pipe to be tested shall be stored at (23 ± 2) °C, or conditioning in accordance with 6.2 shall commence.
If the test is carried out immediately after production of the pipe, a pessimistic result may be obtained. In case of dispute, carry out the test at least 24 h after production and storage at (23 ± 2) °C.
Take as a test piece a pipe (200 ± 20) mm long. Using, for example, a scriber, trace on this test piece two circumferential marks 100 mm apart, corresponding to the test area, at equal distances from the two ends.
Prepare a total of three similar test pieces per pipe sample.
Pipes of diameter 250 mm or larger may be cut into four even segments for production of test pieces.
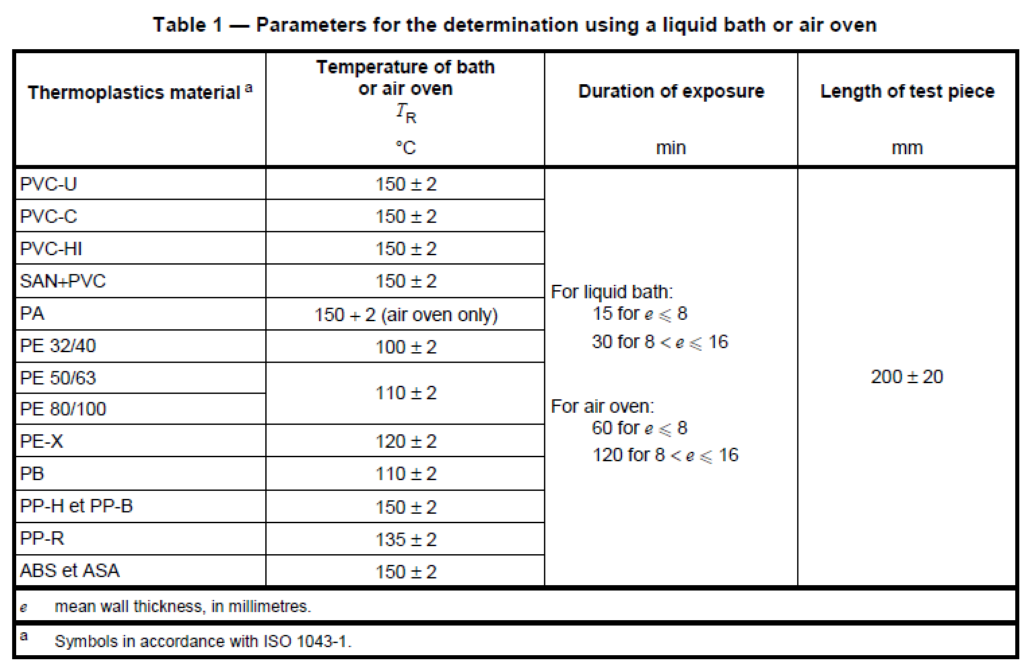
6.2 Conditioning
Condition the test pieces at (23 ± 2) °C for a period of time according to the wall thickness of the pipe as
follows:
>= 1 h, for e < 3 mm
>= 3 h, for 3 mm <= e < 8 mm
>= 6 h, for 8 mm <= e <= 16 mm
where e is the mean wall thickness in millimetres.
7 Procedure
At a temperature of (23 ± 2) °C, measure the distance L0 between the marks to within 0,25 mm.
Set the temperature of the heating bath or air oven to the temperature TR, as specified in Table 1, unless
otherwise specified.
Suspend the test pieces allowing free movement in the heating bath or air oven so that they touch neither the walls nor the base of the bath or oven, and in the case of the bath so that there is a minimum distance of 30 mm between the upper boundary of the test area (see 6.1) and the fluid–air interface. Alternatively the test piece may be supported providing this does not inhibit reversion.
Leave the test pieces for the duration specified in Table 1, unless otherwise specified. Maintain the specified test temperature in the zone between the circumferential marks on the test piece.
Remove the test pieces from the bath or oven and allow them to hang freely in the same position. After they have cooled to (23 ± 2) °C, measure the maximum and minimum distance, L, between marks (diametrically opposed), following any curvature of the marked surfaces.
8 Expression of results
For each test piece, calculate the longitudinal reversion, RL,i, as a percentage, using the following equation:
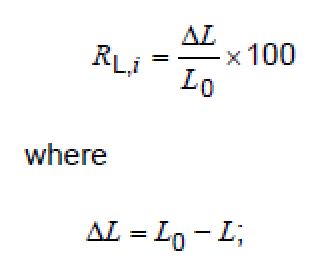
L0 is the distance between the marks before the immersion, in millimetres;
L is the distance between the marks after the immersion, measured along the generatrices, in millimetres.
Choose those measurements of L which give the greatest value of ΔL, with ΔL being either positive or
negative.
When the test piece has been cut into four even segments (see 6.1), the longitudinal reversion of the test
piece, RL,i, is calculated as the average of the three highest of the four results.
Calculate, as the value for the longitudinal reversion RL of the pipe, the arithmetic mean of the values obtained for each of the three test pieces.
Annex A
(informative)
Recommended basic specifications for longitudinal reversion
Using either a liquid bath or an air oven, the calculated value of the longitudinal reversion should conform to the recommended value given in Table A.1.
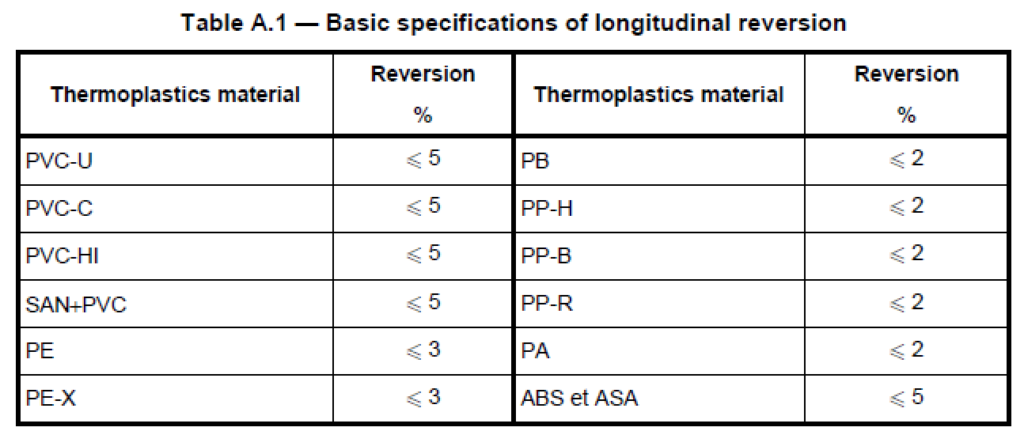
For applications requiring more stringent specifications, a value smaller than the applicable limit given in Table A.1 may be adopted.
Check our YouTube channel for videos of the products, ask any questions on WhatsApp: